Plastic Rotatioinal Molding
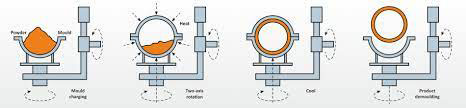
TECHNICAL DESCRIPTION
The Plastic rotational molding process starts with the assembly of the metal molds on the rotating arm. A predetermined measure of polymer powder is dispensed evenly into each mold. It is closed, clamped and rotated into the heating chamber. There it is heated up to around 250oC U820F) for 25 minutes and is constantly rotated around its horizontal and vertical axes.
As the walls of the mold heat up the powder melts and gradually builds up an even coating on the inside surface. The rotating arm passes the molds onto the cooling chamber, where fresh air and moisture is pumped in to cool them for 25 minutes. They continue to rotate at about 20 revolutions per minute throughout the entire process to ensure even material distribution and wall thickness.
Once the parts have cooled sufficiently, they are removed from the molds so that the process can start again. The heating and cooling times, and speed of rotation, are controlled very carefully throughout the process.
TYPICAL APPLICATIONS
Rotation molding is used to produce a variety of products, such as boat hulls, canoes and kayaks, furniture, containers and tanks, road signs and bollards, planters, pet houses and toys.
RELATED PROCESSES
Thermoforming and blow molding can also produce hollow and sheet profiles. Hollow parts produced by twin sheet thermoforming will have a seam where the 2 sheets of material come together. Blow molding is typically used for high volume production of relatively smaller parts, such as thin-walled packaging.
QUALITY
Surface finish is good even though no pressure is applied. The molded product is almost stress free and has an even wall thickness. The plastic will shrink by 3% during the process, which may cause warpage in parts with large flat areas.
DESIGN OPPORTUNITIES
This process is relatively inexpensive for the production of low to medium volume runs and is suitable for small products and large products up to 10 m3 (353 ft3). Some products can be molded in pairs and then separated post-molding to create sheet geometries.
Tooling can be taken directly from a full size prototype in wood, aluminum or resin, which aids the transition between design and production. There is no core in a rotation molding tool, so changes are relatively easy and inexpensive.
Several different types of powder are used to mold shapes that have different levels of complexity. Micro-pellets and fine powders are more suitable for tight radii and fine surface details; however, fine powders show up surface defects more readily. Foam-filled, hollow or other multi-layered walls can be produced with composite polymers, which are triggered at varying temperatures. Wall thicknesses in solid wall sections are typically no more than 5 mm (0.24 in.). Maximum thickness is determined by the temperature of the mold and thermal conductivity of the polymer.
Inserts and preformed sections of different color, threads, in-mold graphics and surface details can be integrated into the molding process. Overmolding of 1 material onto another premold reduces assembly costs and produces seamless finishes. Additives can be used to make the materials UV and weather resistant, flame retardant, static-free or food safe.
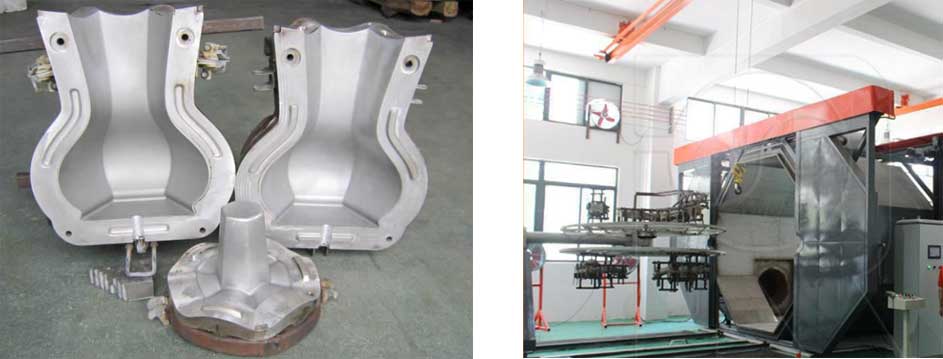