Plastic Injection Molding
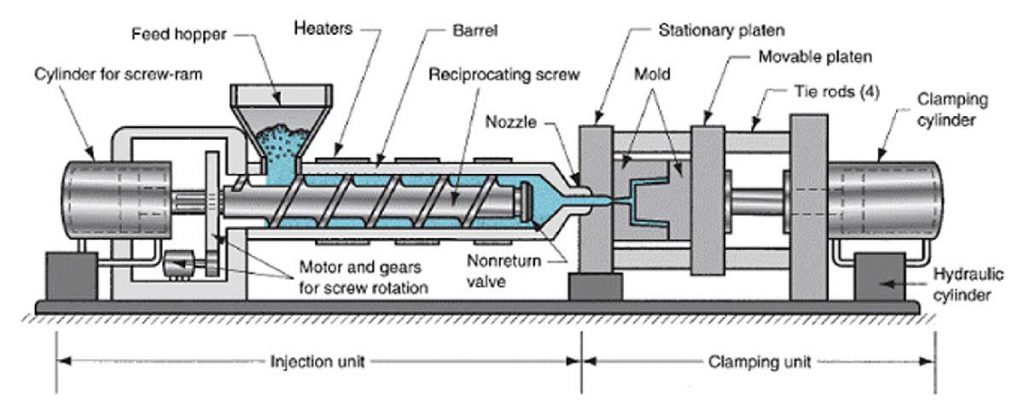
TECHNICAL DESCRIPTION
Polymer granules are dried to exactly the right water content and fed into the hopper. Any pigments are added at this stage at between 0.5% and 5% dilution.
The material is fed into the barrel, where it is simultaneously heated, mixed and moved towards the mold by the rotating action of the Archimedean screw. The melted polymer is held in the barrel momentarily as the pressure builds up ready for injection into the mold cavity.
The correct pressure is achieved and the melted plastic is injected into the die cavity. Cycle time is determined by the size of the part and how long the polymer takes to resolidify, and is usually between 30 and 60 seconds.
Clamping pressure Is maintained after injection to minimize warpage and shrinkage once the part is ejected.
To eject the part, the tools move apart, the cores retract and force is applied by the ejector pins to separate the part from the surface of the tool. The part is dispensed onto a conveyor belt or holding container, sometimes by a robotic arm.
Tools and cores are generally machined from either aluminum or tool steel. The tools are very complex parts of the injection molding process. They are made up of water-cooling channels (for temperature control), an injection point (gate), runner systems (connecting parts) and electronic measuring equipment which continuously monitors temperature. Good heat dispersal within the tool is essential to ensure the steady flow of melted polymer through the die cavity. To this end, some cores are machined from copper, which has much better conductive qualities than aluminum or steel.
The least expensive injection molding tooling consists of 2 halves, known as the male tool and female tool. But engineers and toolmakers are constantly pushing the boundaries of the process with more complex tooling, retractable cores, multiple gates and multi-shot injection of contrasting materials.
INTRODUCTION
Injection molding is a widely used and well-developed process that is excellent for rapid production of identical parts with tight tolerances. It is used to create a huge diversity of our day-to-day plastic products. Accurately engineered tools and high injection pressures are essential for achieving excellent surface finish and reproduction of detail. Consequently, this process is suitable only for high volume production runs.
TYPICAL APPLICATIONS
Injection-molded parts can be found in every market sector, in particular in automotive, industrial and Household products. They include shopping baskets, stationery, garden furniture, keypads, the housing of consumer electronics, plastic cookware handles and buttons.
QUALITY
The high pressures used during injection molding ensure good surface finish, fine reproduction of detail and, most importantly, excellent repeatability. The downside of the high pressure is that the resolidified polymer has a tendency to shrink and warp. These defects can be designed out using rib details and careful flow analysis. Surface defects can include sink marks, weld lines and streaks of pigment. Sink marks occur on the surface opposite a rib detail, and weld lines appear where the material is forced to flow around obstacles, such as holes and recesses.
DESIGN OPPORTUNITIES
So much is practically possible with injection molding that restrictions generally come down to economics. The process is least expensive when using a simple split mold. Most expensive are very complex shapes, which are achievable in a range of sizes, from large car bumpers to the tiniest widgets. Retractable cores controlled by cams or hydraulics can make undercuts from the sides, top or bottom of the tool simultaneously and will not affect the cost significantly, depending on the complexity of the action.
In-mold and insert film decoration are often integrated into the molding cycle, so eliminating finishing processes such as printing. There is also a range of pigments available to produce metallic, pearlescent, thermochromatic and photochromatic effects, as well as vibrant fluorescent and regular color ranges. Inserts and snap-fits can be molded into the product to assist assembly.
Multi-shot injection molding can combine up to 6 materials in one product. The combination possibilities include density, rigidity, color, texture and varying levels of transparency.
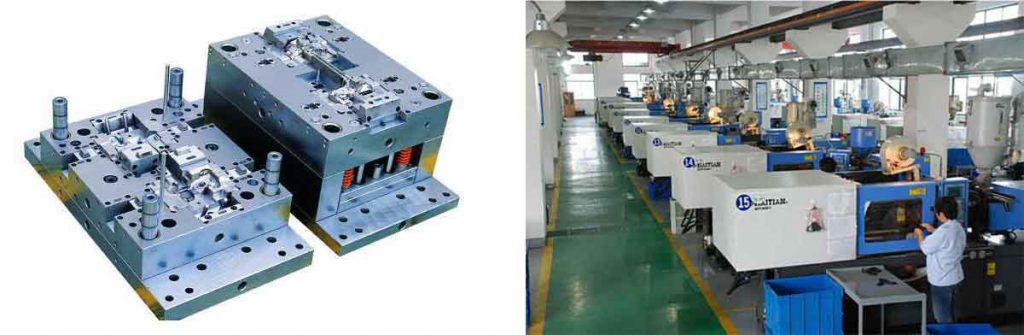