Metal Sand Casting
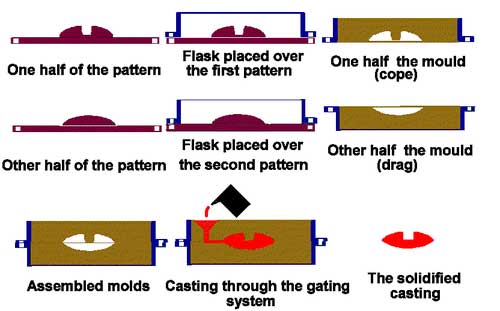
TECHNICAL DESCRIPTION
The sand casting process is made up of 2 main stages: mold-making and casting. In stage 1 the mold is made in 2 halves, known as the cope and drag. A metal casting box is placed over the wooden pattern and sand is poured in and compacted down.
For dry sand casting the sand has a vinyl ester polymer coating, which is cured at room-temperature. The polymer coating on each sand particle helps to achieve a better finish on the cast part because it creates a film of polymer around the pattern, which forms the surface finish in the cast metal. For green sand casting, the sand Is mixed with clay and water until it is sufficiently wet to be rammed into the mold and over the pattern. The clay mix is left to dry so that there is no water left in the mix. Water must be removed because otherwise it will boil and expand during casting, thereby causing pockets of air in the mold.
Meanwhile, sand cores are made in separate split molds and then placed in the drag. The runner and risers, which are covered with an insulating sleeve, will already have been built into the pattern.
In stage 2, the 2 halves of the mold are clamped together with the cores in place. The metal is heated up to several hundred degrees above its melting temperature. This is to ensure that during casting it remains sufficiently molten to flow around the mold. A predetermined quantity of molten metal is poured into the runner, so it fills the mold and risers. Once the mold is full an exothermic metal oxide powder is poured into the runner and risers, which burns at a very high temperature and so keeps the metal at the top of the mold molten for longer. This means that as the metal inside the mold solidifies and shrinks as it cools it can draw on surplus molten metal in the runner and risers. Porosity on the surface of the part is therefore minimized.
INTRODUCTION
Sand casting is a manual process used to shape molten ferrous metals and non-ferrous alloys. It relies on gravity to draw the molten material into the die cavity and so produces rough parts that have to be finished by abrasive blasting, machining or polishing.
The sand casting process uses regular sand, which is bonded together with clay (green sand casting) or synthetic materials (dry sand casting) to make the molds. Synthetic sand molds are quicker to make and produce a higher quality surface finish. However, the quality of the casting is largely dependent on the skill of the operator in the foundry.
There are many variables in the casting process that the designer can do nothing about, although properly designed parts with sufficient draft angles will result in higher quality parts.
Sand casting is most commonly used to shape metals. Glass can also be cast in this way, but because of its high viscosity it will not flow through a mold.
Evaporative pattern casting is a hybrid of the sand casting and investment casting processes, and it can be inexpensive. Instead of a permanent pattern, evaporative pattern casting uses an expendable foam pattern (often polystyrene), which is embedded in the sand mold. The foam pattern is typically formed by CNC machining or injection molding. The molten metal burns out the foam pattern as it is poured in. Parts made in this way have inferior surface finish, but this technique is very useful for prototyping, one-off and manufacturing very low volumes.
TYPICAL APPLICATIONS
Sand casting is used a great deal in the automotive industry to make engine block and cylinder heads, for example. Other applications include furniture, lighting and architectural fittings.
QUALITY
The quality of surface finish and mechanical properties depend largely on the quality of the foundry. For example, nitrogen is pumped through molten aluminum to remove hydrogen, which causes porosity. When the parts are removed from the sand molds the surface finish is distinctive, so all cast parts are blasted with an abrasive. Varying grits are used to produce the highest quality finish. Parts can then be polished to achieve very high surface finish. Because sand casting relies on gravity to draw the molten material into the mold cavity, there will always be an element of porosity in the cast part.
COSTS
Tooling costs are low for one-off and low volume production, the main cost being for patternmaking, which is inexpensive compared to die casting tooling. Low cost patterns can be machined in wood or aluminum. Foam patterns for the evaporative pattern method are the least expensive of all.
Cycle time is moderate but depends on the size and complexity of the part. Casting usually takes less than 30 minutes, but secondary and finishing operations increase cycle time.
Labor costs can be high, especially as the majority of this process is manually operated and the quality of casting is affected by the skill of the operator.
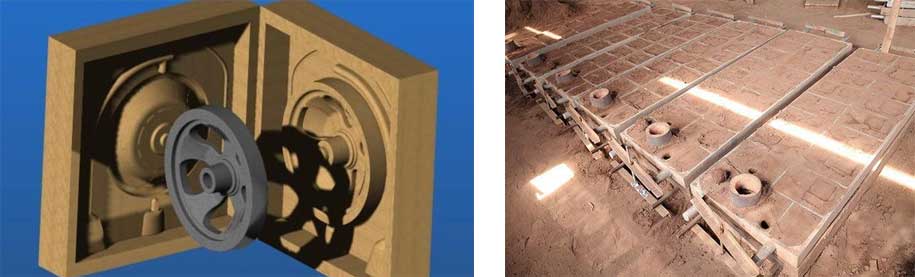